Injection plastique
Exemple de pièce : Boîte à air
Matériau : Thermoplastique ABS
Principe de fonctionnement
Un système de vis sans fin pousse des grains de thermoplastique dans un tube chauffé. Ces grains "fondent" et la pâte obtenue est injectée dans un moule en métal préalablement usiné. Le plastique refroidit dans le moule et garde la forme de la cavité de ce dernier. Le moule s'ouvre ensuite et la pièce est éjectée, pour débuter un autre cycle.
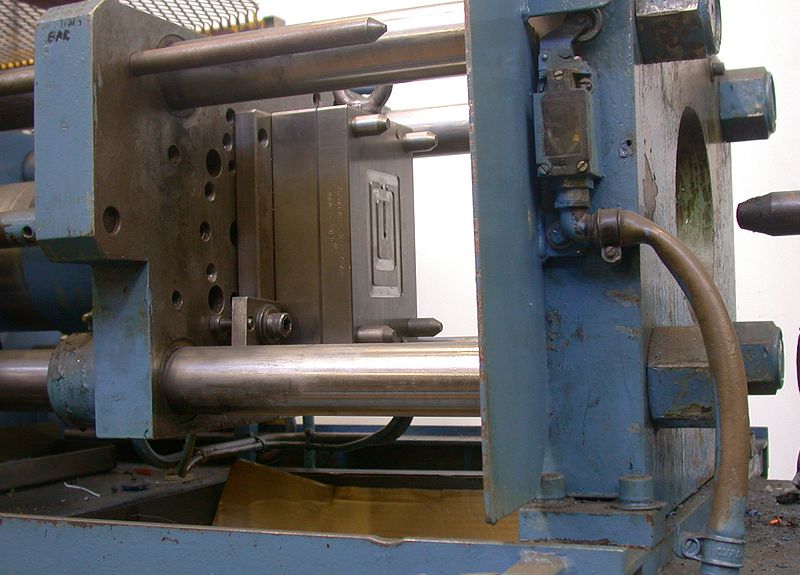
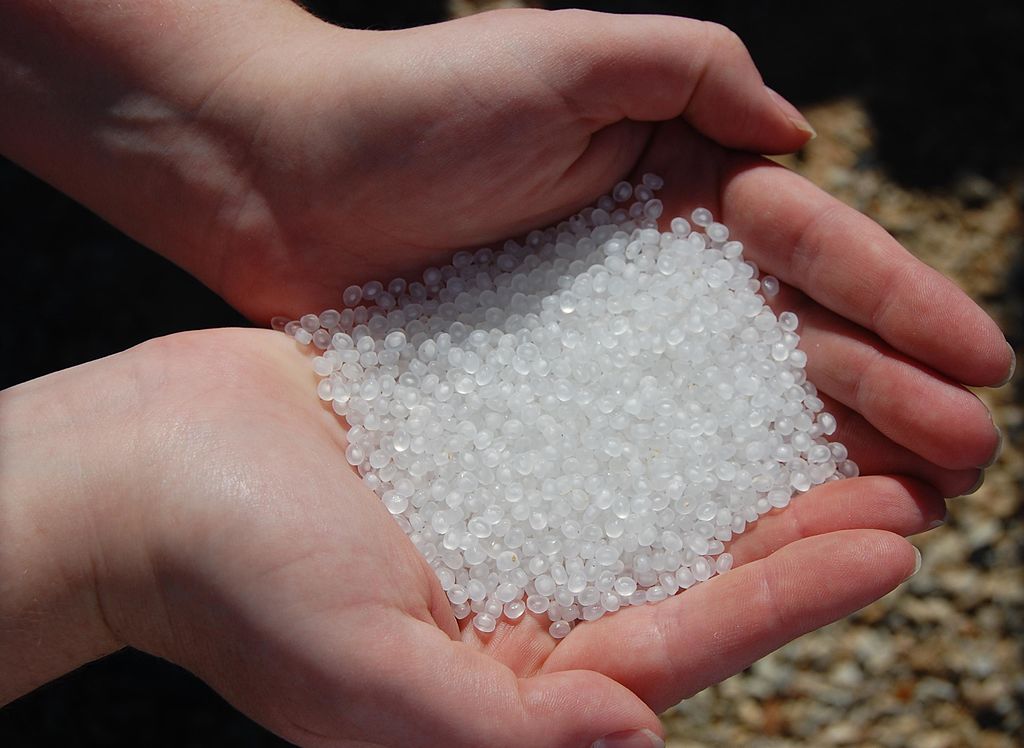
Pourquoi ces matériaux et méthodes ?
Avantages
Très léger (peu dense)
Facile à produire
Etat de surface très bon
Cela permet de limiter le poids du moteur et donc de faciliter la tâche à l'utilisateur
Les pièces réalisées en injection plastique sont peu coûteuses, du fait du prix du matériau, et de la grande cadence de production
Enlevant ainsi le besoin d'un traitement de surface supplémentaire (ponçage, peinture...)
Inconvénients
Faible résistance mécanique
Faible résistance thermique
Impératifs sur la forme
Grand investissement
Il est impossible de créer de formes supportant de hautes contraintes, comme des filets (ceux-ci sont mis en place à l'aide d'inserts métalliques intégrés à la pièce)
Le placement de la pièce dans le moteur devra prendre en compte cette propriété (Il faut éviter le pot d'échappement qui peut devenir chaud)
La forme de la pièce doit être moulable, posséder des dépouilles. De plus, la pièce possèdera un plan de joint.
Le moule d'injection est coûteux, et n'est rentable que lors de la fabrication d'une grande quantité de pièces. Ce moteur ayant été produit en série,
Moulage en coquille
Exemple de pièce : Cylindre moteur
Matériau : Aluminium
Principe de fonctionnement
Un moule en plusieurs parties est rempli d'alumium en fusion. L'aluminium refroidit et de fige dans la forme contrainte par le moule. On peut ensuite ouvrir le moule pour en extraire la pièce. On le referme avant de recommencer.
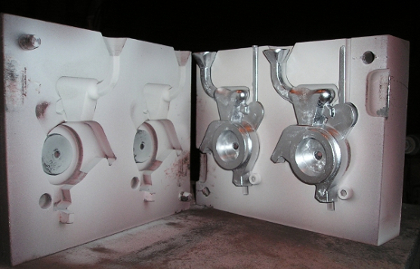
Pourquoi ces matériaux et méthodes ?
Avantages
Relativement léger (peu dense),
Conducteur thermique
Conducteur électrique
Facilité de formage
Cependant, suffisamment résistant à la chaleur et aux contraintes liées aux explosions.
Cela est nécessaire pour refroisir le moteur par air via les ailettes.
Cela est nécessaire pour permettre à la masse de la bougie d'être connectée à la bobine.
Le moulage coquille permet une plus grande cadence que le moulage au sable ou à cire perdue
Il offre un meilleur état de surface que le moulage sable, qui sera conservé sur les surfaces non fonctionnelles.
Par rapport à l'usinage monobloc, économise la matière en réduisant les chutes, est moins coûteux en outils.
Inconvénients
Surfaces fonctionelles nécessitent d'être usinées ensuite
Un plan de joint sera présent
Crée des impératifs sur la forme
La forme générale foit être moulable (convexe), il doit y avoir des dépouilles (visibles sur les ailettes)
Emboutissage de tôles
Exemple de pièce : Pot d’échappement
Matériau : Acier doux
Principe
Une tôle plate est prise entre 2 moitiés de matrice, dont la forme est conçue en fonction de celle de l'objet voulu. Une presse applique une force aux matrices, ce qui déforme plastiquement la tôle et lui donne la forme désirée. Ici, plusieurs pièces sont serties ensemble pour créer une seule pièce : le pot d'échappement.
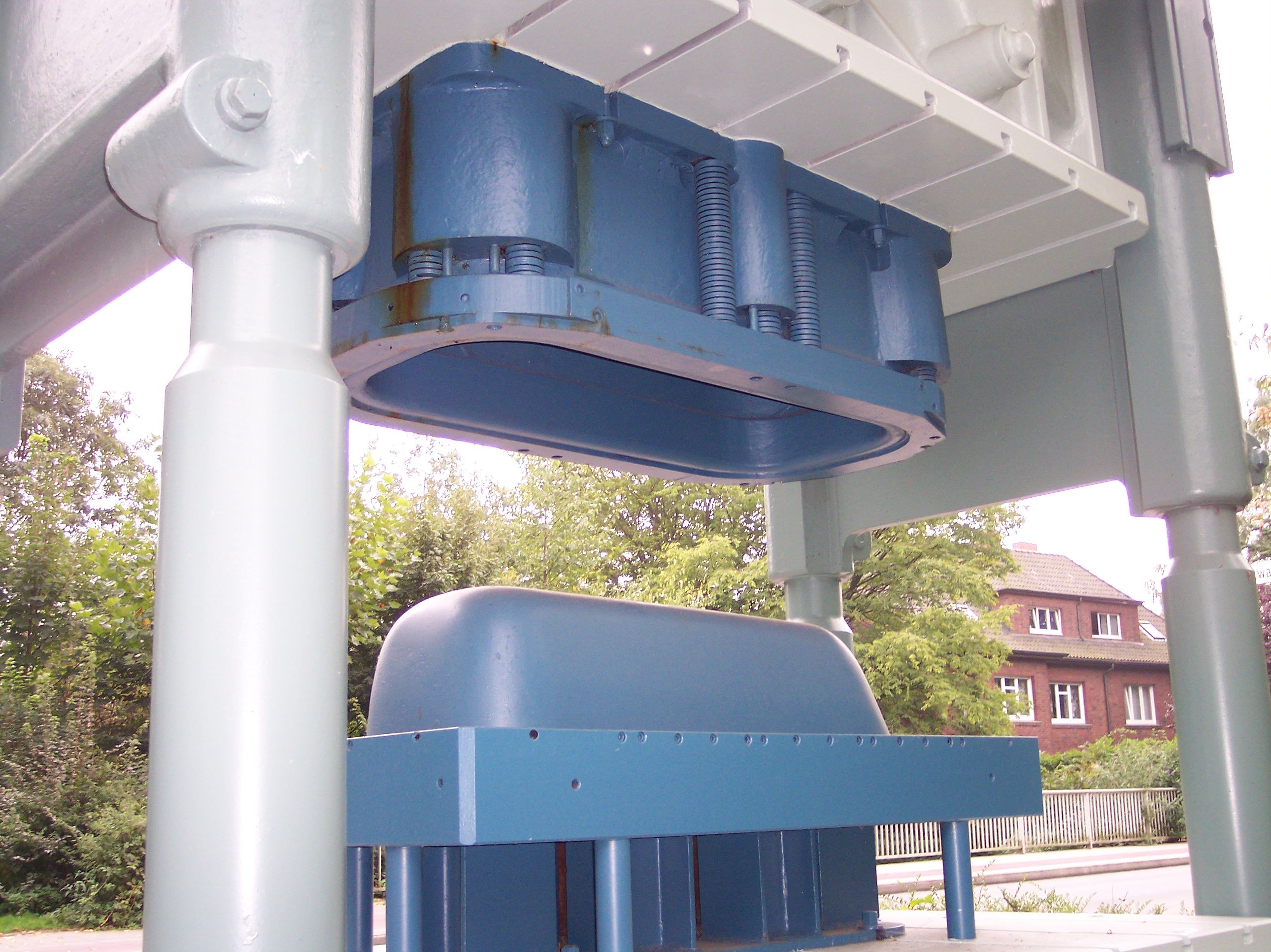
Quels procédés de mise en forme ?
- Débouchage
- Emboutissage
- Sertissage
Pourquoi ces matériaux et méthodes ?
Avantages
- Résistant à la chaleur
La tôle est un des matériaux les moins coûteux qui résiste aux chaleurs endurées à l'échappement
- Grande cadence
Ce procédé crée les pièces à la chaîne à grande cadence. Cela permet de produire une grande quantité de pièces en peu de temps.
- Prix bas
Bien que l'investissement dans le matériel et l'outillage soit important, le prix par pièce résultant est très bas.
Inconvénients
- Précision moindre
La précision d'un tel procédé n'égale pas celle de l'usinage
- Peu de liberté dans la forme
La forme de la pièce doit suivre plusieurs contraintes : la présence de dépouilles, la forme doit être convexe.